Polyethylene Embossed Foil
Rubber Separator for Tire Manufacturers, Vulcanized Rubber and Composite Materials
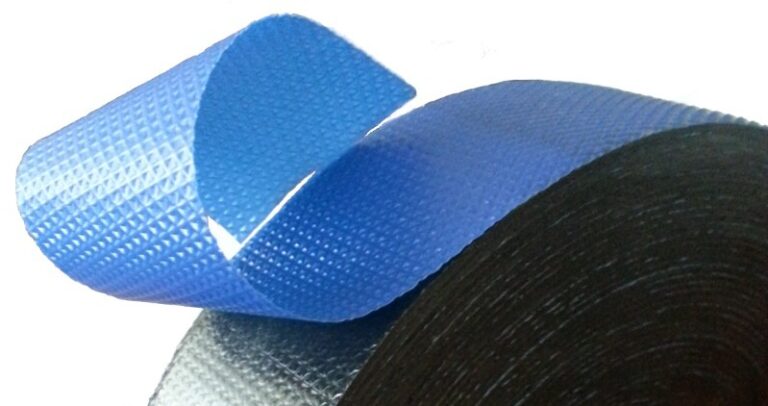
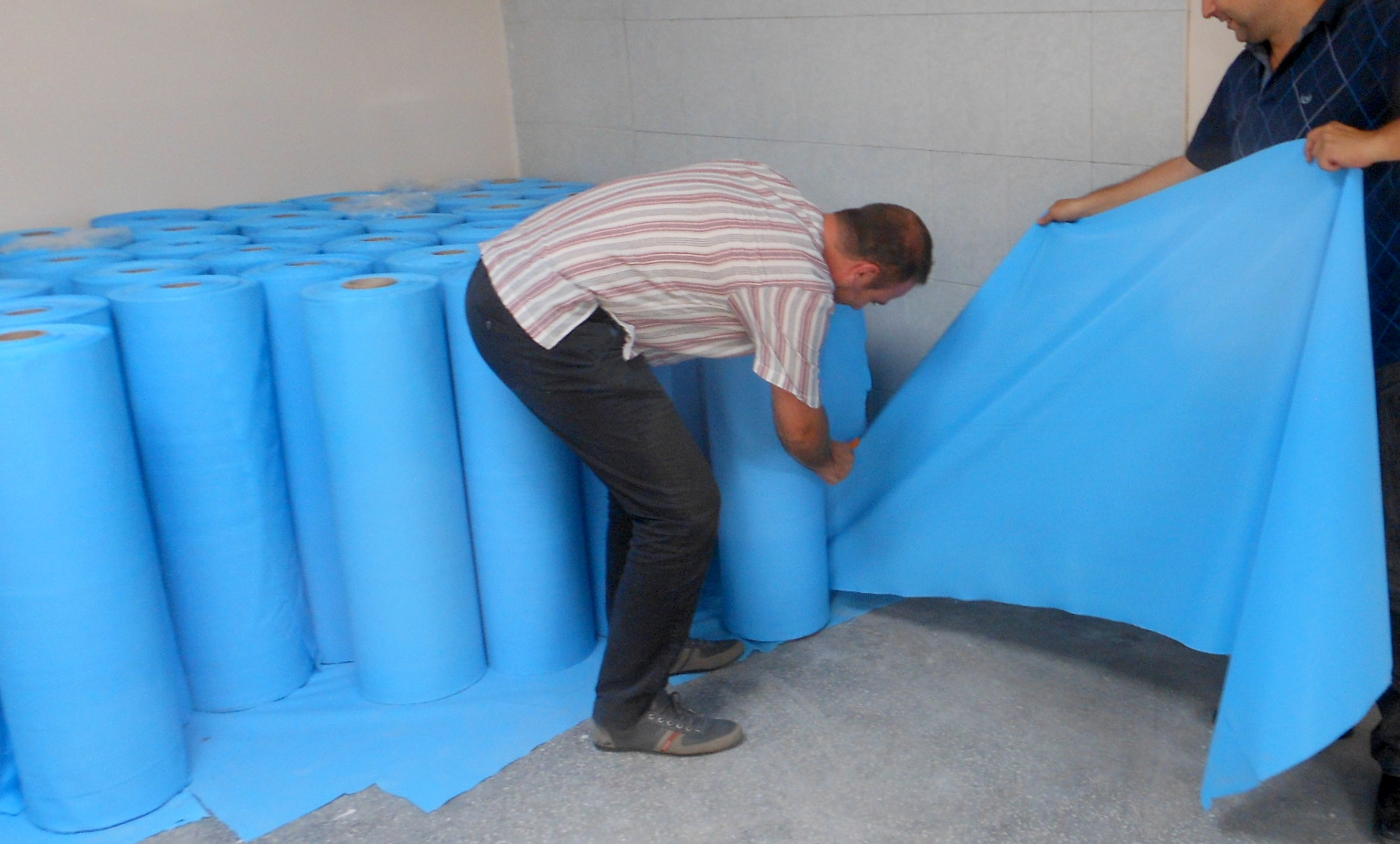
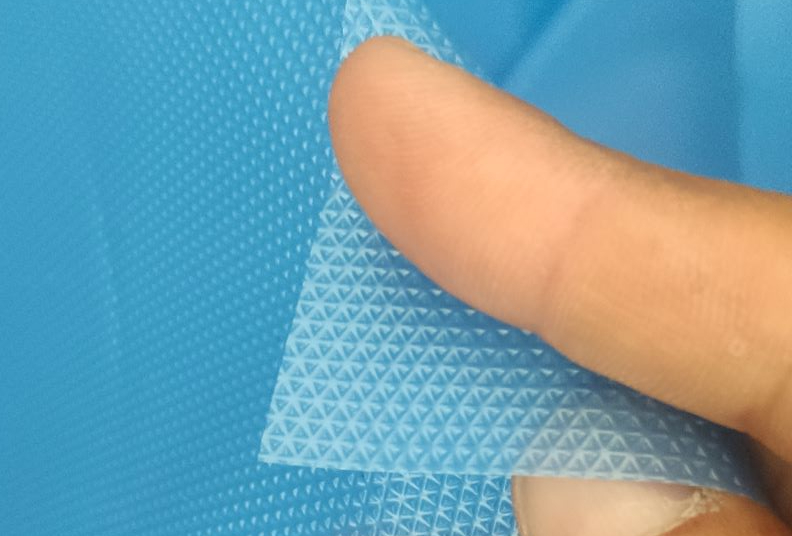
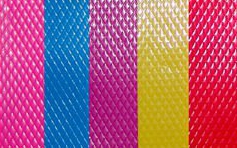
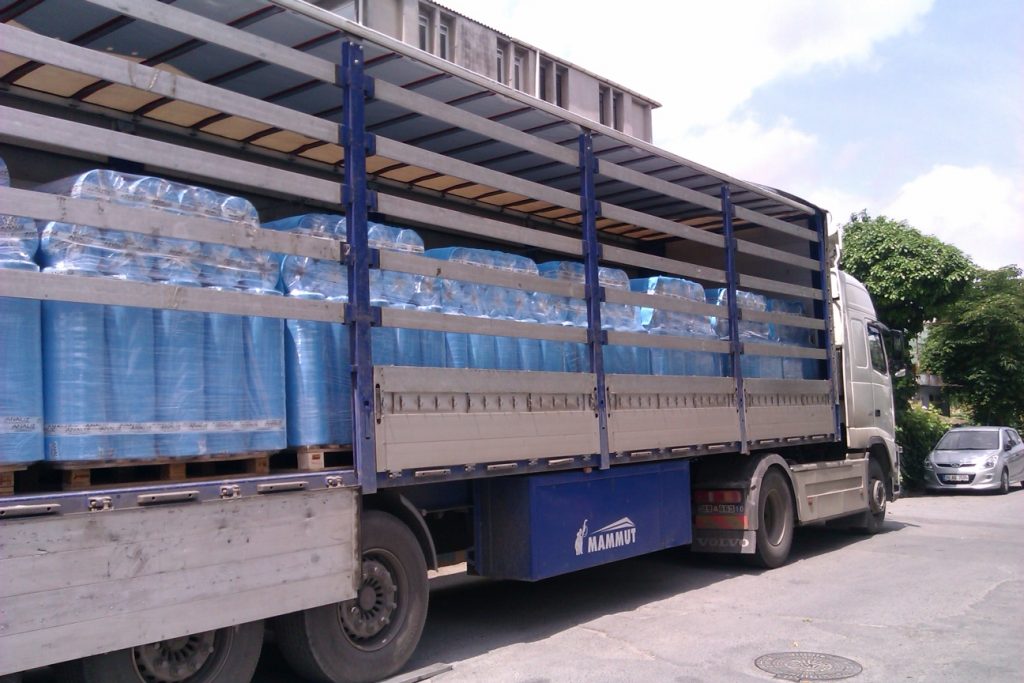
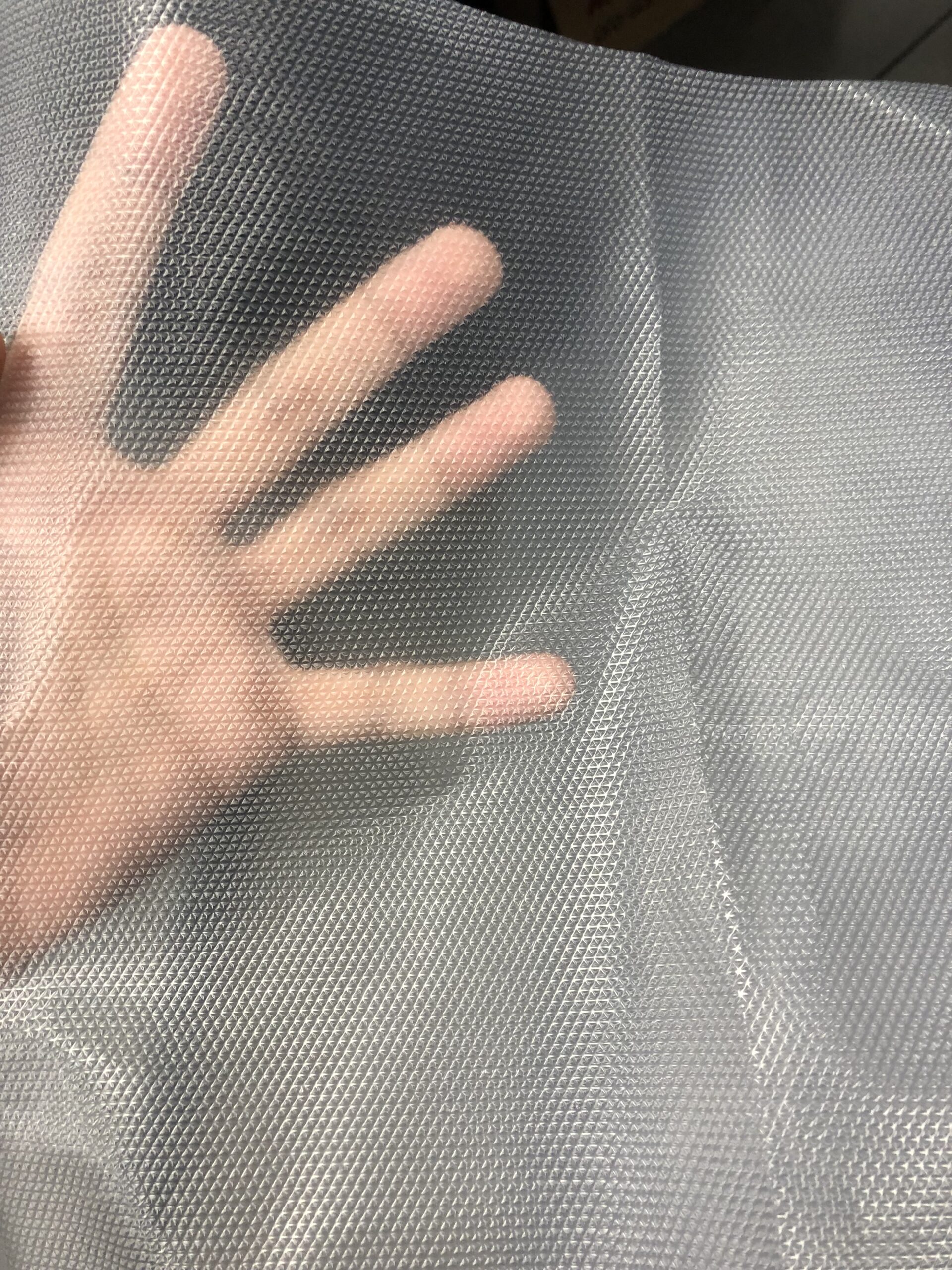
Tire and Vulcanized Rubber Production
The embossed polyethylene film is used as a release layer in the processing of rubber compounds, including:
- Tire production: inner liner, sidewall and rubber compound separator
- Easy storage for calendered rubber
- Separator for extruded rubber sheets
Composite MATERIALS : PREPREG SEPARATOR
In composite materials, the embossed polyethylene film is used in as a separator for prepreg materials. It prevents adhesion between the sheets of prepreg materials.
- Clean, defect-free prepreg sheets
- Easy to store, easy to detach
- Better prepreg quality
Benefits of Polyethylene Embossed Foil
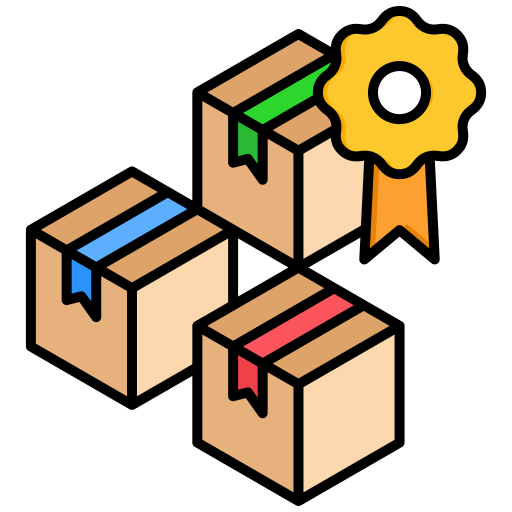
Improved Product Quality
Protects from abrasion, contamination and foreign substances to ensure a smooth, uniform surface finish and enhance overall product quality
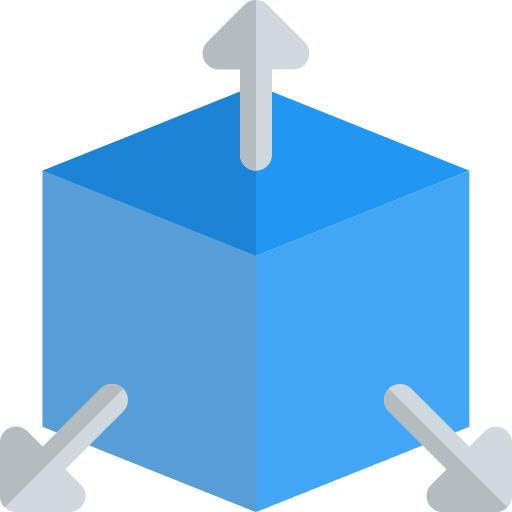
Enhanced Mold Release
The embossed surface creates a barrier that facilitates easy release, minimizing production downtime and waste.
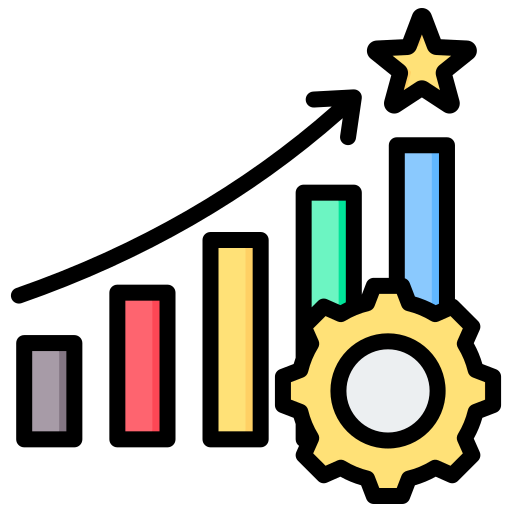
Increased Efficiency
Streamlines the manufacturing process, reducing the need for additional release agents or manual interventions.
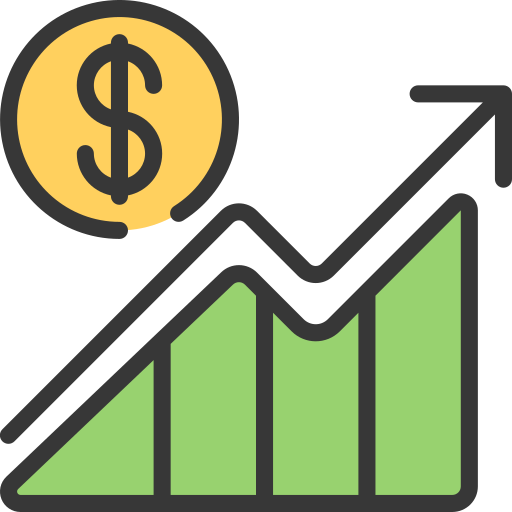
Cost-Effective Solution
In the rubber calendering process it is used as a separator of rubber sheets. It does not stick or melt and is easy to remove.
Technical Specifications: Polyethylene Embossed Foil
- PRODUCT: Diamond embossed PE film
- MATERIALS: LDPE + MDPE + colour masterbatch (we do not use any silicone, fatty acids or metallic salts of fatty acids)
-
DIMENSIONS AND TOLERANCES:
- Thickness before embossing (DIN 53370): 0,08 – 0,10 mm ± 12 %
- Thickness after embossing (DIN 53370):
• 0,08 mm -> 0,320 - 0,380 mm
• 0,09 mm -> 0,330 - 0,400 mm
• 0,10 mm -> 0,340 - 0,410 mm
- Width:
• 500 - 800 mm ± 5 mm
• 801 - 1200 mm ± 7 mm
• 1201 - 1600 mm ± 10 mm -
PHYSICAL CHARACTERISTICS:
- Melting point: 100 - 110 °C
- Tensile strength:
• MD: > 20 MPa
• TD: > 19 MPa - Elongation at break:
• MD: > 250 %
• TD: > 350 % -
PACKAGING:
- Core: carton, 76 mm
- Pallet: per customer request
* Reels are delivered on a pallet and wrapped with stretch film. Each reel is marked with a control label; each pallet is equipped with a numbered pallet sheet.
STORAGE
-
Storage conditions:
products must be stored in a dry area and should not be exposed to direct sunlight. Recommended storage conditions include temperatures between 10 °C and 25 °C and relative humidity between 40 % and 60 %. Any deviations in temperature and humidity may lead to altered product properties. - Shelf life: In cases described above regarding the recommended storage conditions, the estimated shelf life is 1 year from the date of production.
Mechanical properties
- Machine direction >14,7 MPa (N/mm2)
- Transversal direction >10,8 MPa (N/mm2)
- Machine direction: >150 %
- Transversal direction: >250 %
- Melting point: 90-130 °C
An environmentally-friendly alternative: polyester-based multilayer film
This new release liner is a stiff polyester-based multilayer film that is reinforced internally with a high tear resistance mesh; the film is then embossed in a second step to increase its release properties. With very high tear resistance, excellent mechanical qualities and release properties for processes that require a stiffer film.
High Mechanical Strength and Tear Resistance
Excellent release qualities for rubber
Costs less - can be reused 20-25 times more than conventional products
More environmentally friendly than standard polyethylene liner
Preserves fresh rubber sheets, without creases or deformation
No polluting substances, fraying or bagging
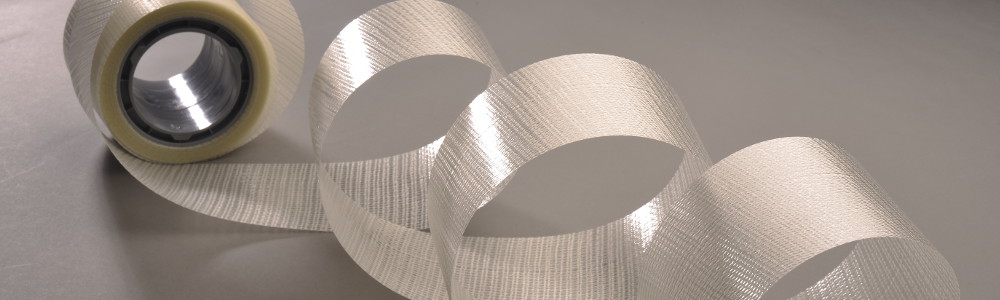
Contact Us
Have a question or want to explore a collaboration? Fill out the form below and we’ll reply shortly.